Technical Advantages of CQB Magnetic Drive Pumps in High-Temperature, High-Pressure Boiler Feedwater Systems
1. Key Features of Magnetic Drive Pumps
- Seal-less Design: Utilizes magnetic coupling transmission (isolated sleeve + permanent magnets), eliminating shaft seal leakage risks. Ideal for high-temperature, high-pressure, toxic, or costly media.
- High Safety: Avoids leaks caused by mechanical seal wear, ensuring water quality integrity and reducing downtime.
- High-Temperature Resistance: Specialized materials (e.g., neodymium iron boron magnets, silicon carbide isolation sleeves) withstand media temperatures ≤350°C.
- Low Maintenance: Non-contact transmission minimizes wear, extending service life.
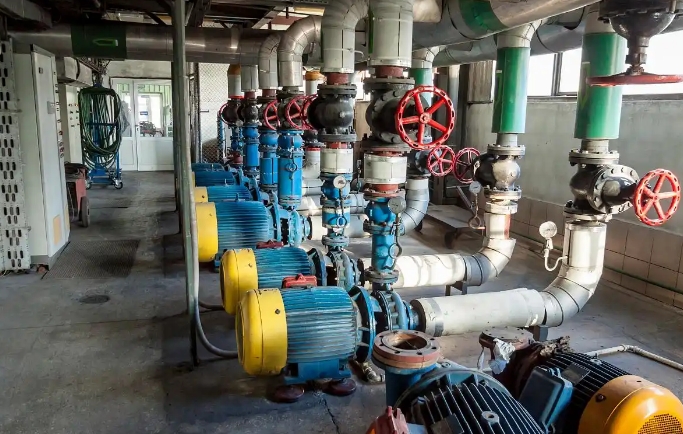
2. Technical Adaptability in Boiler Feedwater
- High Pressure & Temperature:
- Designed for pressures 1.6–20 MPa with multi-stage impellers or reinforced casings.
- Cooling systems (e.g., water-cooled jackets) or heat-resistant magnets ensure stability in high-temperature environments.
- Anti-Cavitation Design:
- Optimized impeller inlet flow paths and inducer vanes reduce NPSHr, preventing vaporization.
- Material Selection:
- Stainless steel (304/316) or duplex steel components resist chloride ions and corrosive media.
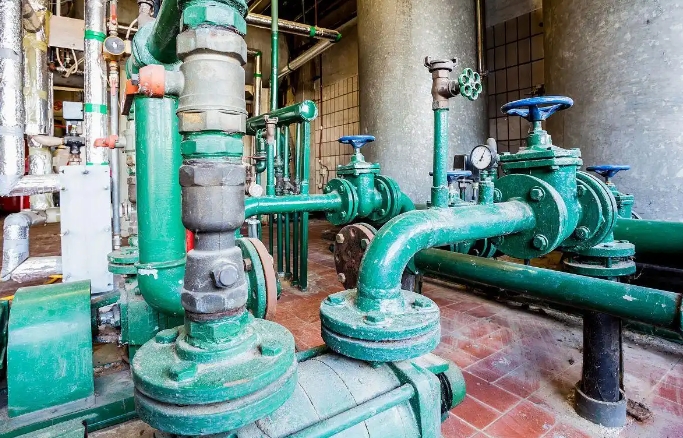
3. Applications in Boiler Systems
- Steam Boiler Feedwater: Pressurizes deaerated water into steam drums (e.g.CQB-type magnetic drive pumps).
- Hot Water Circulation: Ensures leak-free operation in closed-loop heating systems.
- Chemical Dosing: Safely transfers anti-scale agents or pH regulators without leakage.
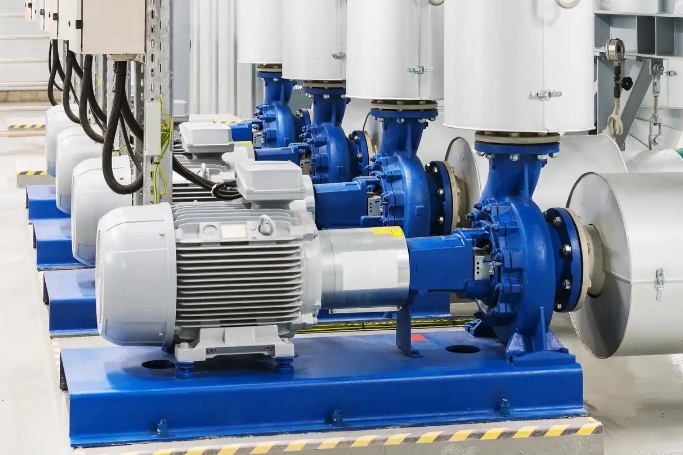
4. Selection & Operation Guidelines
- Key Parameters:
- Flow range: 5–500 m³/h (adjustable based on boiler capacity).
- Head range: 20–800 m (matches system pressure and piping resistance).
- Temperature limit: -20°C to 350°C (select models based on media temperature).
- Energy-Saving Configuration:
- Integrate with VFDs to adjust speed based on load, reducing energy consumption by 20–40%.
- Installation Requirements:
- Install inlet filters (≥80 mesh) to protect against debris.
- Maintain minimum continuous flow to prevent dry running or overheating.
5. Maintenance & Troubleshooting
- Daily Monitoring:
- Track bearing temperature (≤80°C) and vibration (≤4.5 mm/s).
- Ensure cooling lines are unobstructed.
- Scheduled Maintenance:
- Inspect isolation sleeve thickness every 6 months (replace if wear exceeds 30%).
- Test magnetic flux every 2 years (replace driver if attenuation > 15%).
- Common Issues:
- Reduced Flow: Clean impeller or check magnet demagnetization.
- Abnormal Noise/Vibration: Realign pump-motor shafts or replace bearings.
Comparison: Magnetic Drive Pumps vs. Mechanical Seal Pumps
Criteria |
Magnetic Drive Pumps |
Mechanical Seal Pumps |
Leakage Risk |
Zero leakage |
Potential leaks over time |
Maintenance Cost |
Low (no seal replacement) |
High (periodic seal repairs) |
Media Compatibility |
Hazardous/expensive/corrosive |
Water/low-risk media |
Initial Cost |
Higher |
Lower |
Energy Efficiency |
High (no friction loss) |
Moderate (seal friction loss) |
Case Study
- Chemical Plant Steam Boiler Upgrade:
- Replaced leak-prone mechanical seal pumps with AHJN CQB Magnetic Drive Pump (Model: CQB50-32-250):
- 8,000 hours of leak-free operation.
- 18% energy savings (VFD + optimized impeller).
- 60% reduction in annual maintenance costs.
Conclusion
CQB magnetic drive pumps, with their zero-leakage design, high reliability, and low maintenance, are revolutionizing boiler feedwater systems—especially in industries prioritizing safety and sustainability. Critical factors include temperature/pressure compatibility and material selection, while VFD integration maximizes energy efficiency. For legacy boiler upgrades, CQB pumps deliver long-term stability and lifecycle cost savings.